When developing the RN30, Hyundai’s designers and engineers established a new approach to reducing weight and lowering the center of gravity. Instead of using carbon fiber reinforced polymer (CFRP) common to most high-performance cars, Hyundai broke the mold with all-new high-performance plastic materials, developed in collaboration with a leading global chemical company. For example, due to their outstanding flowability, BASF’s systems developed for body panels permit the realization of even those most challenging designs like the fender and spoiler of the RN30. Combining high quality with low weight, they can even directly be painted thanks to their Class A surface. The RN30 also features semi-structural sandwich solutions for the trunk floor, providing a considerable weight reduction as well as a highly efficient production process.
These weight-saving innovations are light, highly durable and environmentally-friendly and are used throughout the new concept to help boost handling and acceleration. Inside, redundant parts were removed, while heavier parts sit in the lowest possible position. The center of gravity is lowered further by pushing back and lowering the seats, with all these elements combining to achieve a light weight, ideal for performance driving.
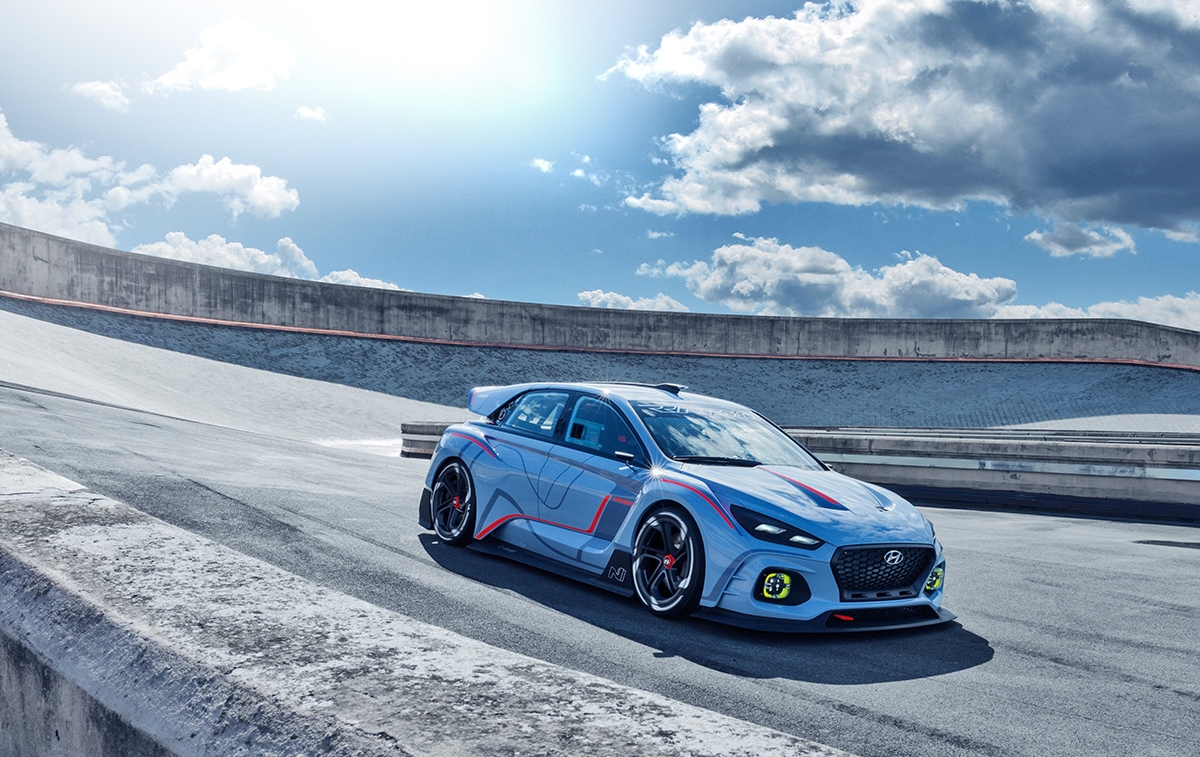