Il monitoraggio strutturale (SHM) è una disciplina sempre più impiegata per il controllo di elementi come ponti ed edifici realizzati in acciaio o cemento armato. Nel settore dei compositi la tecnica è utilizzata da anni per conseguire obiettivi diversi, come la prevenzione di guasti sulle strutture provocate da carichi eccessivi, per ridurre la frequenza delle ispezioni, e quindi dei costi, di manufatti in servizio, o per conoscere in tempo reale l’evoluzione di una frattura.
Un importante risultato in questo campo è stato ottenuto con il progetto Smartfiber (finanziato nell’ambito del Settimo programma quadro dell’Unione Europea), appena conclusosi, che dopo 4 anni di studi e ricerche ha portato allo viluppo di un sistema completo di sensori miniaturizzato, da integrare in una struttura composita, nel caso specifico una turbina tidal, da utilizzare per la generazione di energia pulita dal mare.
L’approccio scelto dai ricercatori ha previsto l’integrazione nella struttura in composito di un sistema di sensori Fiber Bragg Grating (FBG) e di un interrogatore miniaturizzato a basso costo, con alimentazione wireless e comunicazione a due vie con un’unità di lettura esterna.
Altro notevole risultato ottenuto dai partner del progetto, che comprende, l’istituto belga IMEC, Ghent University, Optocap, Xenics (Leuven, Belgio), Fraunhofer Institute for Integrated Circuits, FBGS International (Geel, Belgio) e Airborne International, è stato il piazzamento automatico dei sensori e dell’unità interrogatore nella fase di produzione della struttura.
Anzi, proprio questa esigenza ha spinto i ricercatori ad optare per l’impiego di sensori FBG, invece che altre tecniche di monitoraggio della deformazione, come i più classici estensimetri elettrici. Infatti, i sensori FBG, oltre ad assicurare un monitoraggio continuo, risultano leggeri, compatti, sono immuni alle interferenze elettromagnetiche e presentano un’elevata resistenza alla corrosione e alla temperatura.
La fotonica del silicio ha permesso la miniaturizzazione dell’interrogatore FBG, con costi molto contenuti, il cui nucleo è costituito da un circuito integrato che trasmette un segnale che, dopo l’elaborazione, viene ricevuto dall’unità di lettura esterna. Quest’ultima fornisce anche l’alimentazione wireless all’interrogatore. Altro componente chiave dell’interrogatore è il filtro Array Waveguide Grating. Tutti dispositivi che possono essere realizzati utilizzando consolidate tecniche industriali di miocrofabbricazione del silicio.
Il sistema completo, dopo la connessione a una catena di sensori in fibra ottica, è stato integrato all’interno della pala della turbina di marea, una costruzione a sandwich con anima in schiuma e pelli di tessuto non-crimp.
La lama è stata fabbricata con la tecnica LRTM, (Light resin transfer molding) e, per ridurre al minimo l’accumulo di resina intorno al sistema integrato e ridurre il brusco cambiamento di rigidezza dal laminato ai dispositivi incorporati, sono stati aggiunti altri strati in tessuto di vetro.
Ulteriori strati di tessuto di vetro sono stati collocati per minimizzare l’accumulo di resina intorno al sistema integrato e ridurre il brusco cambiamento di rigidezza dal laminato agli elementi incorporati. La fibra ottica è stata posata lungo tutta la lunghezza della lama ed è stata sviluppata un tecnica per il suo posizionamento automatico.
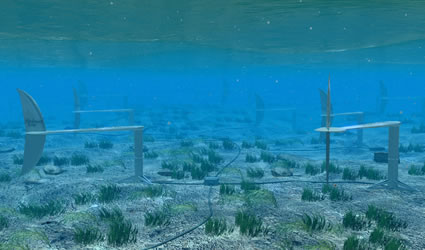