Fabrizio Rosi – TEC Eurolab Srl
Marco Salvador e Nicola Guidolin – STEP Lab Engineering Snc
L’interesse per la risposta ad impatto dei materiali compositi è cresciuto notevolmente dopo la seconda metà degli anni ’60, fenomeno determinato dall’introduzione dei materiali compositi rinforzati con fibra di carbonio. Diversamente dai GFRP, che mostrano una buona risposta meccanica quando sottoposti a test di impatto, i CFRP necessitano di indagini più approfondite, data la natura fragile della fibra di carbonio.
Poiché la principale causa di danneggiamento di strutture in composito viene causata dall’impatto di corpi estranei, come nel caso della superficie alare di velivoli, l’impatto di un grave su di una superficie piana rappresentativa del materiale è stato adottato come metodo di test principale per valutare i danneggiamenti da impatto.
Tuttavia, il test di impatto non restituisce direttamente informazioni correlabili al meccanismo di danneggiamento del componente testato. Pertanto, un insieme di metodi di indagine post impatto si rende necessario per potere determinare le modalità di propagazione della rottura e di fallimento del componente. Di seguito viene riportato un esempio di valutazione del danneggiamento occorso mediante tomografia industriale.
Le prove di impatto sono state realizzate mediante torre d’impatto DW 1000 realizzata da Step Lab. La macchina permette di eseguire prove con altezza di caduta da 0.05 a 1.25 m. Modulando opportunamente il peso dell’impattatore, è possibile ottenere energie di caduta che spaziano da 5 a 750 J.
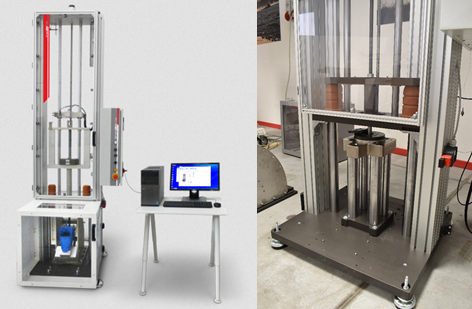
Le prove sono state eseguite in accordo alla normativa ASTM D7136/D7136M-12. I provini vengono vincolati su un supporto dedicato, l’operatore imposta l’energia di impatto nel software di controllo, e un sistema pneumatico preleva automaticamente l’impattatore e lo porta all’altezza corrispondente. L’impattatore viene quindi rilasciato in caduta libera fino a colpire il provino con la sua testa emisferica avente diametro 16 mm. Generalmente, la sequenza di prova proposta viene identificata come metodo CAI (Compression After Impact).
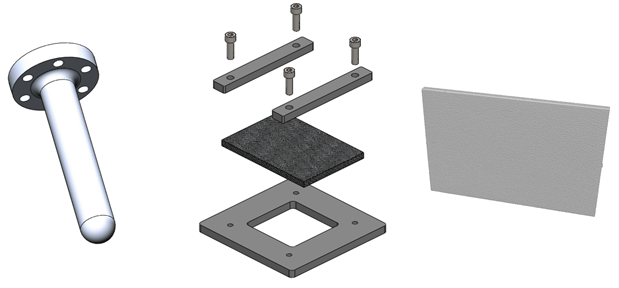
Durante l’esecuzione di un test di impatto vengono acquisite posizione, velocità ed accelerazione dell’impattatore. A partire dai dati acquisiti viene calcolata la resistenza ad impatto del materiale: il profilo di accelerazione, moltiplicato per la massa dell’impattatore, fornisce infatti la forza sviluppata durante l’urto. Il software integra la curva forza-spostamento ed ottiene l’energia assorbita dal provino durante l’impatto, ovvero la sua resilienza.
Lo scopo delle prove eseguite è stato quello di sottoporre il provino ad un impatto di energia predefinita, in funzione del suo spessore, e di studiarne successivamente i meccanismi di cedimento attraverso la tomografia computerizzata. Le curve di posizione, velocità, forza ed accelerazione possono quindi essere utilizzate per una valutazione diretta delle caratteristiche del materiale o possono servire come strumento utile per l’integrazione di informazioni all’interno di un modello, che può essere validato mediante un software di simulazione ad elementi finiti.
Il software di acquisizione e di elaborazione è in grado di analizzare urti di brevissima durata (6-7 ms), tipici di provini in materiale composito, caratterizzati da elevata rigidezza.
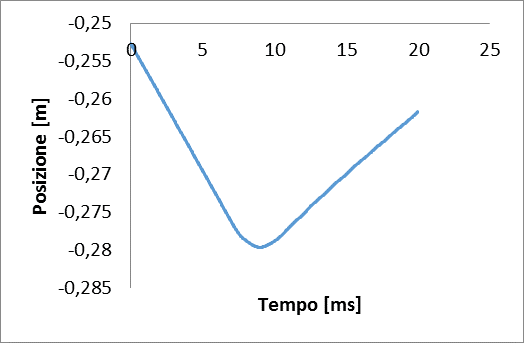
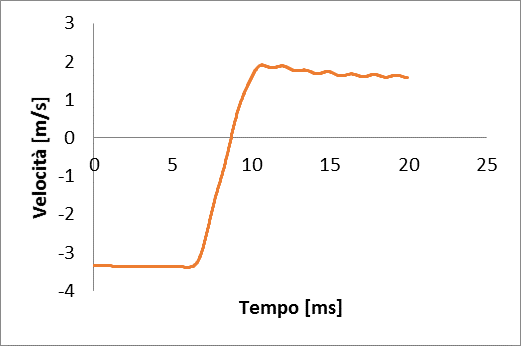



La figura 3 riporta le curve ottenute dall’impatto su uno dei provini. Si noti la breve durata dell’urto e l’elevata forza sviluppata durante l’impatto.
Le figure 4 e 5 documentano il risultato degli impatti sulle due tipologie di campioni testati. Le medesime tipologie di danneggiamento rilevate da un’indagine visiva superficiale sono presenti anche all’interno del campione, come è possibile vedere dall’indagine tomografica.
I campioni testati sono stati sottoposti a scansione tomografica prima e dopo l’impatto. Sono state analizzate due tipologie di campioni realizzati con differenti sequenze di laminazione e dimensione di trama ed ordito.
Il test è stato realizzato mediante un tomografo NSI X5000, impostando i parametri elettrici ed operativi riportati in tabella.
Il tomografo sfrutta la capacità della radiazione x di attraversare la materia, generando una serie di radiografie che vengono ricomposte, tramite uno specifico algoritmo, nel volume interno ed esterno dell’oggetto analizzato. In tal modo, diventa possibile valutare approfonditamente dei danneggiamenti interni di componenti, senza alterare in alcun modo il componente analizzato.

Dalle immagini tomografiche è possibile analizzare i diversi tipi di difetti sviluppatisi e classificarli in accordo alla normativa ASTM D7136/D7136M-12. A livello visivo, è stato possibile rilevare la presenza di una depressione superficiale post impatto, accompagnata da varie fratture combinate di grandi dimensioni con rottura delle fibre. L’analisi tomografica consente di indagare la propagazione della rottura attraverso i diversi strati del provino. Nella figura 7 sono riportate quattro sezioni progressive del campione A analizzato dopo l’impatto. Come risulta evidente, l’indagine tomografica permette di andare a valutare puntualmente le modalità di propagazione della frattura, contribuendo sensibilmente ad incrementare la comprensione dei meccanismi di danneggiamento, senza alterare permanentemente lo stato del campione.

1- Fig.1: Torre di caduta DW 1000 utilizzata per i test
2- Fig.2: Impattatore a testa emisferica 16 mm, Holder e sequenza di montaggio del campione di prova e volume tomografico del campione A testato
3- Fig.3: Esempi di curve di posizione, velocità, accelerazione e forza ottenute dall’impatto del campione di prova B e dati relativi ai due campioni analizzati