The new process, called gel electrospinning, is described in a paper by MIT professor of chemical engineering Gregory Rutledge and postdoc Jay Park. Basically, Rutledge explains that usually when you get high strength, you lose something in the toughness, but in the fibers made by the new process, many of those tradeoffs are eliminated, getting a material that has very high strength and high toughness. With this process, which uses a variation of a traditional method called gel spinning but adds electrical forces, the results are ultrafine fibers of polyethylene that match or exceed the properties of some of the strongest fiber materials used for applications including bullet-stopping body armor. High-performance fibers are also used as reinforcing fibers in some high-performance composites. Compared to carbon fibers and ceramic fibers, which are widely used in composite materials, the new gel electro spun polyethylene fibers have similar degrees of strength but are much tougher and have lower density. Most plastics are tough, but they’re not as stiff and strong as desired, and glass fibers are stiff but not very strong, while steel wire is strong but not very stiff. The new gel electro spun fibers seem to combine the desirable qualities of strength, stiffness, and toughness in ways that have few equals. The researchers’ process combines the use of a polymer gel as the starting material, as in gel spun fibers, but uses electrical forces rather than mechanical pulling to draw the fibers out; the charged fibers induce a “whipping” instability process that produces their ultrafine dimensions. And those narrow dimensions, it turns out, led to the unique properties of the fibers. These results might lead to protective materials that are as strong as existing ones but less bulky, making them more practical.
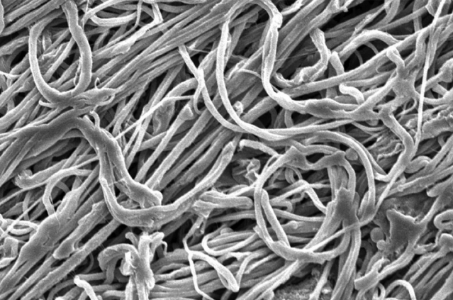