A new study has shown that graphene is able to withstand far more current than we previously anticipated – and way more than regular material – making it the perfect building block for next-generation ultra-fast electronics.
“The current density is around 1,000 times higher than that which would lead to the destruction of the material under normal circumstances,” said one of the researchers, Elisabeth Gruber, from the Institute of Applied Physics at TU Wien in Austria.
“But over these distances and time scales, graphene can withstand such extreme currents without suffering any damage.”
To clarify, what we’re talking about here is not how efficiently graphene can conduct electricity. Earlier last year, scientists already managed to turn the material into a superconductor, capable of shuttling electrons with zero resistance.
This latest study looked not at the efficiency of electron flow, but just how much current the material could handle – specifically, how many electrons it could handle charging through it in a short space of time. And the results are impressive.
In case you need a quick refresher, graphene is a one-atom thick, honeycomb-latticed sheet of carbon that displays some incredible properties on the nano scale. It’s stronger than steel, harder than diamond, and incredibly flexible – and now it appears to be capable of withstanding high charge density.
To figure this out, the researchers blasted positively-charged xenon ions at a sheet of graphene, causing large numbers of electrons to be ripped away from the graphene where they smashed through. Just imagine these xenon ions ripping away graphene’s electrons like throwing a tennis ball at a dusty sheet.
A single xenon ion could steal more than 20 electrons from a tiny area of the graphene film, which might not sound like much, but seeing as each carbon atom only has six electrons to start with, that’s a pretty big deal for the stability of the material.
As a result, the surrounding carbon atoms were left extremely positively charged.
The xenon ion also punches an entire carbon atom out of the graphene sheet as it passes through, but this has a much smaller affect than the loss of all those electrons. In a normal material, electrons would rapidly try to fix the imbalance, but it couldn’t happen quickly enough, so the material would start to break down.
“What you would expect to happen now is for these positively charged carbon ions to repel one another, flying off in what is called a Coulomb explosion and leaving a large gap in the material,” said team member Richard Wilhelm from the Helmholtz-Centre Dresden-Rossendorf in Germany. “But astoundingly, that is not the case. The positive charge in the graphene is neutralised almost instantaneously.”
So graphene is somehow capable of filling its gaping electron hole with brand new electrons almost instantly, meaning it’s transporting a hugely high density current in a short period of time.
And when we say short period of time, we mean it – those new electrons rushed in to save the day in mere femtoseconds (quadrillionths of a second).
“The electronic response of the material to the disruption caused by the xenon ion is extremely rapid,” said Gruber.
“Strong currents from neighbouring regions of the graphene film promptly resupply electrons before an explosion is caused by the positive charges repelling one another.”
The amount of current density graphene has to carry to make that happen is around 1,000 times higher than any normal material could tolerate.
Further research is needed to understand exactly how this happens, but it’s incredible news for engineers wanting to build ultra-fast electronics in the future, because graphene might be the one material durable enough to handle such intense electron flows. “The hope is that for this very reason, it will be possible to use graphene to build ultra-fast electronics. Graphene also appears to be excellently suited for use in optics, for example in connecting optical and electronic components,” said team leader Fritz Aumayr.
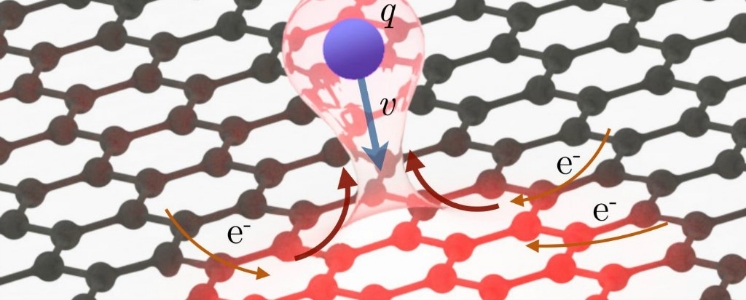