The “missing link” in Australia’s carbon fibre capability, a wet spinning line, has been launched in a ceremony at Waurn Ponds just outside Geelong.
Carbon fibre combines high rigidity, tensile strength and chemical resistance with low weight and is used in aerospace, civil engineering, the military, cars, and also in competitive sports. Only a handful of companies around the world can create carbon fibre, each using their own secret recipe.
To join this elite club CSIRO and Deakin researchers had to crack the code.
In doing so, using patented CSIRO technology, they’ve created what could be the next generation of carbon fibre that is stronger and of a higher quality.
Director of CSIRO Future Industries, Dr Anita Hill, said the development was an important milestone.
“This facility means Australia can carry out research across the whole carbon fibre value chain: from molecules, to polymers, to fibre, to finished composite parts,” Dr Hill said. “Together with Deakin, we’ve created something that could disrupt the entire carbon fibre manufacturing industry.”
Deakin University Vice-Chancellor, Professor Jane den Hollander AO said the development is a great example of what Deakin and CSIRO could achieve together, for the benefit of all of Australia.
“Our two organisations share a long-standing and distinguished bond, one that our new Strategic Relationship Agreement (SRA) deepens even further,” Professor den Hollander said. “Together, we’re conducting industry focussed research with a profound and lasting impact, from the communities we serve, through to the world.”
The wet spinning line machinery takes a sticky mix of precursor chemicals and turns it into five hundred individual strands of fibre, each thinner than a human hair. They’re then wound onto a spool to create a tape and taken next door to the massive carbonisation ovens to create the finished carbon fibre.
The CSIRO/ Deakin wet spinning line was custom built by an Italian company with input from the organisations’ own researchers.
The company liked the design so much it made another for its own factory and the the CSIRO/ Deakin machine has been described as “the Ferrari of wet spinning lines”. Assistant Minister for Industry, Innovation and Science the Honourable Craig Laundy MP officially launched the facility.
“This is a great example of how collaboration in the Australian research sector can accelerate research, lead innovation and provide new job opportunities,” Mr Laundy said. “Geelong already has a global reputation for industrial innovation. Initiatives such as this enhance that standing.”
Geelong has become a hub for Australian carbon fibre expertise, with companies such as Carbon Revolution and Quickstep Automotive calling it home. Carbon Revolution supplies composite wheels for the Ford GT supercar and Shelby Mustang GT350R, while Quickstep Automotive created the carbon fibre air intake for the Ford Falcon XR6 Sprint.
Quickstep has also announced that it has received a $1.45m government grant to develop carbon fibre composite seats for automotive applications.
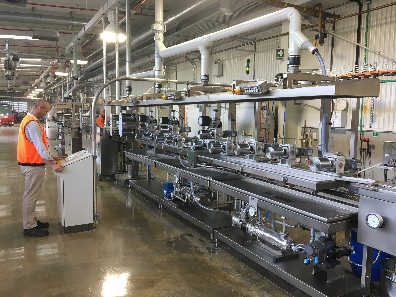