3D printing’s usefulness is growing at a staggering rate. Automotive startup Local Motors is taking this new technology to the extreme: it’s just introduced the LM3D Swim, the first 3D-printed car aimed for mass production. The all-electric LM3D Swim comprises approximately 75 percent 3D-printed parts, but the company aims to increase that number to 90 percent as the technology continues to develop. The Swim’s body is the result of a crowd-sourced contest that ended in July and the build was completed in September. Taking just over two months from design to prototype, Local Motors built a 3D-printed car at unprecedented speed. The company is continually testing new types of materials and different blends for additive manufacturing. As of now, it’s using a blend of 80 percent ABS plastic and 20 percent carbon fiber.
The LM3D was built with a focus on further optimizing the construction methodology of Direct Digital Manufacturing. With the LM3D series, early tests show promise that all crash testing will be complete by the end of 2016 including all certifications needed to get 3D-printed cars on the road. In fact, company’s goal is to make 3D-printed cars safer than traditionally manufactured cars.
In order to ensure compliance, but more importantly consumer safety, the underpinnings of the vehicle throughout the series will remain the same. However, company plans to offer a wide range of customizable, aesthetic features that are only possible through DDM and 3D printing. Cars could look radically different but be built on the same platform.
Speaking of speed, the company is operating on quite the fast timeline. Initial deliveries are slated for 2017, at an estimated retail price of $53,000.
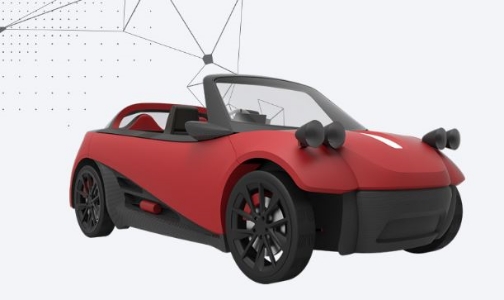