Il McLaren Composites Technology Centre (MCTC), nuovo centro di eccellenza dedicato allo sviluppo ed alla produzione di componenti in fibra di carbonio, sarà operativo dal 2019 a Sheffield, la città del South Yorkshire che è una realtà di primo piano nello sviluppo di nuove tecnologie, anche in virtù della presenza di uno degli atenei universitari più importanti oltremanica. Il “new deal” McLaren si prepara in chiave hi-tech: è nel nuovo McLaren Composites Technology Centre che, dall’anno prossimo, verranno prodotte le cellule abitacolo in fibra di carbonio che dal 2009 rappresentano il”marchio di fabbrica” per l’azienda che, all’inizio del 2016, con l’annuncio del “Track 22” aveva comunicato un proprio programma relativo allo sviluppo di una quindicina di nuovi modelli in un’ottica a medio-lungo termine. Un progetto che, come aveva reso noto l’amministratore delegato Mike Flewitt in occasione del Salone di Ginevra 2016, avrebbe previsto un investimento da ben 1,3 miliardi di euro, da distribuire nell’arco di sei anni, e finalizzato esclusivamente alla ricerca, allo sviluppo ed alla produzione della nuova lineup McLaren, che per almeno metà del proprio assortimento sarà costituita da vetture ad alimentazione ibrida. Del nuovo corso per il marchio di Woking fa quindi parte l’impianto di Sheffield, inaugurato nelle scorse ore: la struttura ha richiesto uno stanziamento nell’ordine di 50 milioni di sterline. Attualmente, spiegano i vertici McLaren, una quarantina di tecnici sono già stati inviati sul posto: operano all’interno dell’Advanced Manufacturing Research Centre dell’Università di Sheffield e si occupano di portare avanti i processi di sviluppo per le cellule abitacolo in fibra di carbonio. Una volta a regime, il nuovo McLaren Composites Technology Centre arriverà a contare una forza lavoro da 200 dipendenti. Fiore all’occhiello dell’inaugurazione del nuovo centro di eccellenza per la produzione di componenti automotive in fibra di carbonio è stata la hypercar Senna, presentata ufficialmente nelle scorse settimane e già andata esaurita: l’intera “tiratura”, programmata in 500 unità, ha già infatti trovato i propri acquirenti, che hanno sborsato cifre nell’ordine del milione di euro per ciascun esemplare. La vettura è equipaggiata con l’unità 4.0 V8 biturbo da 800 CV e 800 Nm, a trazione posteriore e cambio a sette rapporti, la cui tecnologia di costruzione fa, appunto, larghissimo impiego della fibra di carbonio sia per la “vasca” centrale, sia per i pannelli carrozzeria e le relative appendici aerodinamiche, così come per le rifiniture abitacolo. Del resto, nel settore hi-tech automobilistico, McLaren è stata una delle primissime realtà ad individuare la fibra di carbonio quale nuovo materiale sul quale sviluppare il proprio expertise nello sviluppo dei telai. Ciò, infatti, è avvenuto nel 1981, quando, in un’epoca nella quale le leghe metalliche continuavano a rappresentare la realtà di allora, le griglie di partenza della F1 hanno visto il debutto della MP4/1, monoposto capostipite di una nuova generazione di telai. La figura McLaren quale realtà di eccellenza nello sviluppo industriale relativo alle applicazioni della fibra di carbonio in ambito automotive va ad aggiungersi, per restare nel settore dei marchi produttori di supercar, all’apertura dell’ACSL–Advanced Composite Structure Laboratory di Seattle, centro di ricerca Lamborghini inaugurato dai vertici del marchio emiliano nell’estate del 2016.
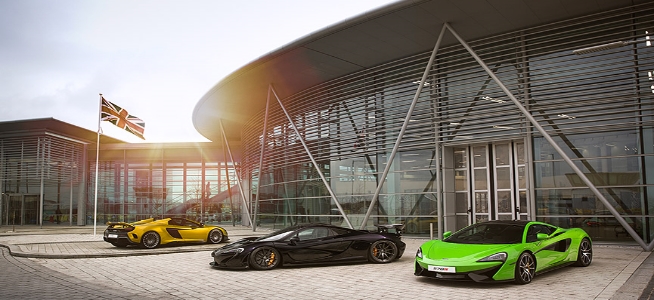