Manufactured from carbon fibre reinforced polymer (CFRP), the wheel is comprised of two components. The centre is made from carbon fibre fabric. This involves cutting and assembling over 200 individual components. The second component is the rim base. This is made from braided carbon fibre by what Porsche claims is currently the world’s largest carbon fibre braiding machine with a diameter of approximately 9 m. The wheel centre is braided into the rim base. The assembled wheel is impregnated with resin and pre-cured at high pressure and high temperatures. The finished wheel is cured at high temperatures followed by a long cooling process. The central lock is then inserted into the finished wheel and the wheel is protected with clear lacquer.
Porsche states it is the first company in the global automotive industry to use this technology. It says braiding offers key advantages over the more conventional method of manufacturing pre-impregnated carbon fibre fabric, making the material structure of the carbon considerably denser and more compact, and increasing rigidity. Using the material more efficiently also produces less waste. The new carbon wheel is made from a total of 18 km carbon fibre or 8 m2 of carbon fibre fabric. From the beginning of 2018, the new carbon wheels will be available as an option for the 911 Turbo S Exclusive Series.
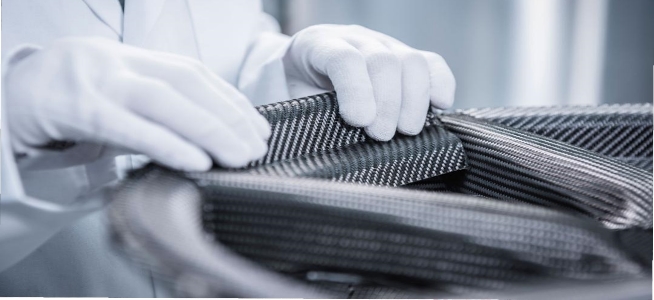