Leg prostheses are much challenging to manufacture. Not only do they need to adequately support the wearer’s weight, they also need to be light enough to enable movement. It’s exactly why the vast majority of leg amputees stick to conventional and very expensive prostheses. But researchers from the Dutch Saxion University of Applied Sciences might have found a digital manufacturing solution, as they have successfully 3D printed leg prosthetics made from thermoplastic composites.
This is a big breakthrough that can certainly decrease the costs of leg prostheses everywhere. Every year, about 2,500 people have a part of their lower limb amputated, and immediately require a customized prosthetic solution to start rehabilitation. Right now, these prostheses are usually made by hand from thermohardening composites and shaped by hand. As these prosthetics carry the person’s weight around all day, they also need to be fitted with a hand-made leg socket – which further increases weight and costs.
But as this research project 3D Comp from Saxion (involving multiple research groups) and several local specialists (including the Rehabilitation Centre ‘t Roessingh) shows, a low-cost and much faster alternative is on the horizon. Right now, fitting procedures are time-consuming and strenuous for everyone involved, but the researchers found that 3D scanning can provide a much more comfortable fit. “The first step of creating a prosthesis is to measure your stump. This is done with help of a 3D scanner and a sensor sock. This sock is used to determine locations of crucial places, like tendons and bones. Now the sock is placed, a professional can feel the exact location of these points,” they explain. Perfect and quick enough for a rehabilitation sector that needs to reinvent itself.
But the real innovation is in 3D printing. While thermoplastic composites (commonplace in the aerospace and automotive industries) are rarely 3D printed, the Saxion team found that they are more than capable of replacing the conventional thermohardening plastics. They are very lightweight and resistant to exterior influences, and more than strong enough to support the wearer’s weight. Most importantly, they can automate the manufacturing process through 3D printing – removing a significant amount of overhead costs.
So why aren’t these thermoplastic composites used more regularly? Essentially, they are too expensive for the medical sector, in which prosthetics aren’t exactly a financial priority. As a result, plastic processing companies have overlooked medical possibilities for these thermoplastic composites. “At the moment most companies still miss the knowledge about such materials, about the necessary processes and about the associated costs. [But] there is an increasing interest in this group of materials. For applications in other industries and the medical area fiber reinforcement provides groundbreaking opportunities,” the researchers say. “Companies often recognize the advantages of the high quality features of thermoplastic composites (say high stiffness and strength at low material weight, freedom in design and the possibility of function integration).”
If the manufacturing costs for these thermoplastic composites are lowered, they would thus become an excellent option for the production of 3D printed leg prostheses. The custom Saxion 3D printing technique, which uses materials filled with long glass or carbon fibers, is an important step in the right direction.
It’s just one of the results of the 3D-Comp project, which also showed that comparable stiffening materials can be locally applied to a wide range of 3D printable components. “This is an important step in realizing cost reduction of lightweight composite technology. An additional advantage of the stiffening of products is a smaller need for material, which can even result in a shorter cycle time and lower energy consumption,” they conclude.
Among others, the researchers have already looked at reinforcing nozzle components, a 3D printed brace and the application of these thermoplastics on bicycle frames. More applications will likely follow through a second research project, which is currently being prepared. Once again, material innovations are responsible for pushing the 3D printing revolution.
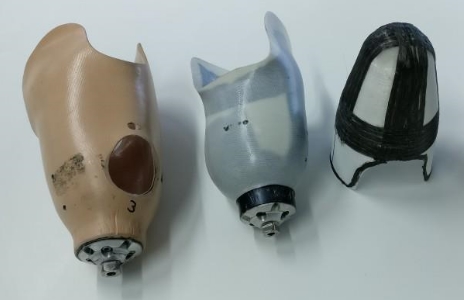