Implants, which help to support broken bones as they heal, have traditionally been made from metals. While this makes the implants strong and resilient, it also means that they have to stay in a body for the rest of a patient’s life unless removed via surgery. While there are advantages to metal implants, medical researchers are constantly looking for more suitable materials which can be more easily absorbed by the body. Evonik, a German chemical specialist which announced details of its 3D printing materials partnership with HP, is a company on the lookout for such materials, and is currently conducting research on new composite materials from which next-generation 3D printed implants can be fabricated.
The high-strength composites being developed by Evonik will have one particularly important characteristic which will set them apart from traditionally used metals: they will be biodegradable, allowing the human body to gradually absorb the material as the bone heals, eliminating the need for invasive surgery to remove the implant. While the company’s research is still in its early stages, the potential benefits to patients are already clear. As well as being biodegradable, specific device designs could also help bones regenerate faster, Evonik says. “In the long term, our focus is regenerative medicine,” explained Dr. Andreas Karau, Head of the Medical Devices Project House in Alabama, where the research is being carried out. “We want to create bioabsorbable implants to replace damaged tissues with healthy tissues. Our current work on biodegradable composites is a first step in this direction.”
Bone fractures can occur for a number of reasons, but with osteoporosis alone accounting for 8.9 million fractures each year, the need has never been greater for high-strength biodegradable implant materials. The materials being developed Evonik will break down in carbon dioxide and water, with devices made from the materials lasting between a few weeks and several months depending on the material’s molecular composition, chain length, and crystallinity. This time will be sufficient for bones to receive the support needed for their regeneration, after which the implant is no longer needed. “Our leading position in polylactic acid-based polymers is an excellent foundation for the development of materials and solutions for regenerative medicine,” Karau said.
Although it has not yet developed products suitable for bone fracture implants, Evonik already has a foothold in medical device production, having delivered its Resomer polymers to medical device manufacturers for use in bioabsorbable screws, pins and small plates. These devices are mainly used for torn knee or shoulder ligaments and for smaller bones in fingers or the face, as their materials are “not strong enough to be used for large, load-bearing bones.” Now, however, the Evonik researchers are looking at composite materials which reinforce biodegradable polymers with inorganic substances, such as calcium phosphate derivatives. These extra elements can make the materials both stronger and more biocompatible.
Although Evonik is not developing its new materials solely for additive manufacturing uses, the company is taking to steps to ensure that its products will be suitable for 3D printing, a technology which can be used to create patient-specific devices. In future, the German chemicals specialist will also look to harness the power of 3D bioprinting technology to create even more advanced medical devices: “In the long term, we intend to develop polymeric scaffolds that could be colonized with living cells–creating a true biological implant,” Karau said.
In addition to its 3D printed medical device research and materials partnership with HP, Evonik recently invested in 3D printed insoles made by Wiiv Wearables, demonstrating the company’s across-the-board interest in additive manufacturing technologies and products.
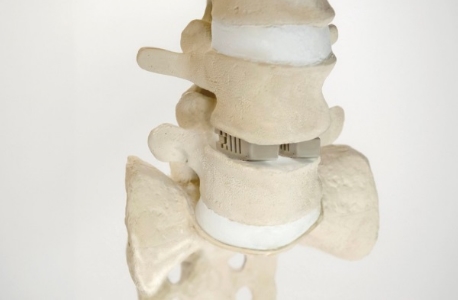